摘要:輕量化設計中異種材料復雜連接構件的需求日益增多,對傳統的連接技術提出了挑戰。塑性連接技術是一種通過材料自身塑性變形實現材料間連接的成形技術,由于其具有生產高效、環境友好、連接穩固等特點,成為近年來國內外學術界和工程界研究的熱點之一。綜述了近年來板材–板材、板材–管材和管材–管材塑性連接新方法,分析了不同塑性連接方法的原理、特點及潛在應用,并對板材、管材塑性連接技術的發展趨勢進行了探討和展望。
關鍵詞:塑性連接;板材–板材連接;板材–管材連接;管材–管材連接;輕量化
隨著能源和環境問題的日益嚴峻,制造業在生產中更加注重“綠色、節能、環保”,輕量化設計已成為現代結構設計中重點考慮的因素之一。在航空、航天、汽車等先進制造領域,以高強鋼、鋁合金、鎂合金及復合材料等為代表的輕質、高強度、難變形材料的應用日益增加。為了能夠最大限度發揮材料的各自優點,異種材料構件在汽車、航空航天等領域應用日益增多,在輕量化設計中有很大比重。然而,異種材料間化學成分、組織等的不同,對傳統的連接工藝帶來了挑戰。如對于焊接性能較差或厚度差別較大的鋁、銅等材料,焊接存在困難,且易發生應力集中。螺栓連接通用性強,但在承受交變載荷或振動工作環境中需考慮防脫落的問題,且螺栓及螺釘頭部進一步增加了連接件的重量。傳統鉚接工藝需要預制孔,降低了原材料強度。采用膠接方法,其連接強度受溫度影響,耐老化性能差。因此,發展面向輕質、高強度、難變形、異種材料間的新塑性成形方法具有廣闊的發展空間。
工程中連接結構的比例極大,同種材料、異種材料間的連接應用廣泛,其中以金屬連接件的應用最多。塑性連接技術是指依靠材料自身的塑性變形流動,實現材料間連接的新型工藝。綜合來說,塑性連接大體可以分為兩類:(1)靠界面壓力實現連接,如利用材料熱脹冷縮進行裝配連接,使用冷棒料作為凸模,沖裁加熱后的板料,實現二者的連接[1],或者利用液壓力實現管材之間的連接[2];(2)機械連接,通過形成機械鎖扣及類似的形式實現連接,如卷邊、自沖鉚接、平板鉚接等。近年來,隨著連接結構的多樣化、連接功能的復合化,出現了許多新的連接方法。與常規鉚釘或其他需要輔助材料的連接方法相比,塑性連接方法通過材料自身變形實現連接,可以有效減重。因此,本文主要對近年來發展的板材、管材間的無輔材塑性連接技術進行介紹。本文首先對近年來提出的板材–板材、板材–管材和管材–管材間塑性連接新方法進行綜述,并分析了各種工藝方法的優缺點及潛在應用前景,在此基礎上,對板材、管材塑性連接技術的發展趨勢進行了展望。鉚接是常見的板材間機械連接工藝之一,無鉚連接和平底鉚接是近年來發展起來的無輔材塑性連接新工藝。然而,無鉚連接在連接點處一側形成凸起,另一側形成凹坑,影響其美觀程度。Chen 等[3]提出了一種用整形鉚釘對鉚接接頭進行整形的新方法,以降低凸出高度,提高連接強度。在整形過程中,將整形鉚釘嵌入到鉚接處,然后用平模在一次行程中壓縮突出部分。通過有限元模擬和試驗研究,優化了整形鉚釘的幾何參數,并驗證了該方法的有效性。由于該方法加入了整形鉚釘,增加了連接件的重量。為了克服這個缺點,進一步提出一種適用于汽車鋁合金板材的平壓整形無鉚連接技術,其原理如圖1所示,通過分瓣式模具和平滑模具獲得平壓整形無鉚連接點,研究表明,平壓整形無鉚連接技術在降低凸起高度的過程中可增加頸厚值,從而有效提高連接點的強度和能量吸收能力,整形力為30kN時,平壓整形無鉚連接點的強度比未整形無鉚連接點的強度增加了16.3%[4–5]。此外,斷裂是平壓整形無鉚連接點的主要失效模式。平底無鉚塑性連接工藝是通過專用的平底無鉚塑性連接模具,利用板材的塑性變形能力,在外力的作用下迫使被連接的板材在連接點處產生材料流動,使板材之間形成一個相互鑲嵌的倒置Ω 形狀的機械鎖,從而實現不同板材之間的連接,且與板材接觸的平底模具的平面是光滑平整的。韓曉蘭等[6]針對平底無鉚塑性連接鉚接頭的抗拉強度檢測成本高、周期較長的問題,建立了平底無鉚塑性連接抗拉強度預測模型,并通過試驗驗證了抗拉強度預測模型的準確性。Gerstmann 等[7]通過數值模擬研究了平底鉚接–粘合混合工藝成形過程,結果表明粘合固化后進一步提高了連接強度,并結合試驗對如何減小粘結劑死區尺寸進行了粘結層厚度、壓邊力等參數優化。圖1 平壓整形原理與連接點剖面對比
Fig.1 Flat-reshaping technology and cross section comparison of joining points圖2 波浪式帶狀鉚釘制造及應用
Fig.2 Method of making wavy ribbon rivet and its application為了達到較高的表面質量和較好的連接強度,Kato 等[8]提出了一種端部預制錐度的管狀鉚釘,放置于板材間并壓縮板材,管狀鉚釘刺穿板材從而實現二者的連接。由于受到擠壓作用,管狀鉚釘的截面變成月牙形,能夠承受較高強度的抗剪及抗拉強度,另外板材表面無凸起,表面質量佳。另外,還提出了一種波浪式帶狀鉚釘制作方法及連接方法(圖2),該鉚釘適用于寬度較大板材間的搭接接頭。采用管狀鉚釘或波浪式帶狀鉚釘的剪切強度達到粘結連接強度的12~14倍。Alves 等[9]進一步研究了不同鉚釘高度、角度對鉚接后互鎖值、鉚釘高度及剪切、拉脫強度的影響規律。但是,管狀鉚釘在連接過程中也會出現鉚釘位置發生轉動的情況,為了解決這個問題,Huang等[10–11]在管狀鉚釘的內側或外側添加了較薄的法蘭,研究了分別具有內、外法蘭的管狀鉚釘連接過程,可有效改善鉚釘鉚接時的轉動問題。碳纖維增強復合材料由于具有較高的比強度、比剛度,輕量化效果明顯,因此也受到越來越多的關注。金屬–復合材料混合結構由于能夠大幅度減輕產品重量、節省燃料,在運輸業、民用基礎設施和建筑業等領域的應用越來越廣泛,實現碳纖維增強復合材料與鋁合金等輕量化金屬材料間的連接具有重要的應用價值。然而,兩種材料間性能的巨大差異,對金屬–復合材料混合結構的連接提出了挑戰。Lambiase 等[12]探討了AA6082–T6/碳纖維增強聚合物(CFRP)薄板的鉚接工藝的可行性,結果表明,采用帶滑動功能的分瓣模來鉚接鋁和碳纖維復合材料薄板是可行的,接頭在破壞試驗中均以脫出的形式失效,因此,頸厚值是鉚接過程中需要重點關注的參數。在此基礎上,提出了兩步鉚接法實現碳纖維增強復合材料與鋁合金之間的有效連接,其成形原理如圖3所示,第1步通過分瓣滑動凹模實現二者的無鉚連接;第2步更換整形模具,通過在凸模下方放置不同高度的圓環,實現不同的整形深度Rd(0.5~2.0mm),整形模具對鉚接點施力并壓縮其高度,研究了整形模具形狀和整形力對鉚接點剪切強度和吸能性的影響規律,采用優化的整形模具獲得的鉚接強度較未整形條件下提高了32%[13]。圖3 金屬 – 碳纖維復合板“兩步法”鉚接原理
Fig.3 Schematic of two-steps clinching of aluminum and carbon fiber reinforced polymer sheets圖4 孔鉚連接工藝原理及連接件截面
Fig.4 Schematic of hole-clinching process and cross-section of hole-clinched joint唐華清等[14]提出了一種金屬與復合材料間的膠–多金屬細針的新型連接方法,并對傳統膠接接頭和膠–多細針接頭進行對比試驗研究,發現新型膠–多細針接頭在極限破壞載荷、破壞應變和能量吸收量等方面均有提高,細針與連接件的橋聯作用力起到抑制膠層開裂的作用,從而提高承載能力和可靠性。Lee 等[15–16]針對高強度、低塑性材料機械連接方面存在的問題,提出了一種“孔鉚連接”新工藝,其連接原理及獲得的連接件截面如圖4所示,首先將韌性材料放置帶有預制孔的脆性材料上方,凸模下壓,韌性材料底部壓薄,并填充凹模型腔,實現鋁合金等材料與先進高強鋼、熱壓鋼、碳纖維增強復合材料等高強度/低塑性材料間的有效連接,通過有限元分析和試驗進一步驗證了該方法的可行性,獲得了達到要求的接頭質量。此外,一些學者也開始借助一些特殊能場來實現板材連接。Babalo等[17]提出一種電液鉚接新方法,將電液成形應用于薄板鉚接中。儲存在脈沖發生器中的電能在浸沒于液體中的電極之間突然放電,并在液體中引發沖擊波,沖擊波使板材變形并形成接頭。采用該方法獲得了0.5mm厚度的AA3105/Ck67 薄板的孔鉚連接件,確定了工藝參數對接頭質量的影響,單搭剪切和剝離試驗結果表明,該連接工藝的應用提高了接頭的強度,其連接效率約為其他孔鉚連接方法的兩倍。激光沖擊鉚接成形新技術(Laser shock clinching,LSC)是一種利用脈沖激光誘發的高壓沖擊波,對板材進行無鉚釘鉚接的新方法,在電子、微制造等領域具有潛在的應用前景。Wang 等[18–19]采用該工藝實現了預制孔不銹鋼板與單層和雙層銅箔之間的連接,圖5為該工藝原理及獲得的不銹鋼板–雙層銅箔的鉚接件,研究表明在合適的激光能量和成形高度下才能獲得良好的連接件,接頭的抗剪強度遠遠大于剝離強度。Wang 等[20–21]利用激光沖擊對1060 鋁箔、銅箔和304 不銹鋼箔進行了微鉚接,通過特定的模具實現對底層箔材的剪切并形成鎖扣結構,并研究了激光能量對頸厚值和最小壁厚的影響規律。Wang 等[22]在無鉚連接中引入一種含碳纖維增強塑料預浸料和鋁粉的夾層結構,應用于碳纖維復合材料板與鋁合金板的連接。研究表明預浸料能有效地填補板材變形產生的空隙,機械聯鎖與樹脂粘接相結合,提高了接頭的可靠性。初明明[23]和趙得鎖[24]等研究了泡沫金屬對壓印-粘接復合接頭力學性能的影響,將泡沫銅、泡沫鎳和泡沫鐵鎳作為復合接頭三明治結構的夾層,分析不同泡沫金屬夾層對Al5052–Al5052 壓印接頭成形質量(峰值載荷、失效位移和能量吸收能力)的影響。針對金屬板材連接成形時在厚度方向上承載能力較差且易產生脫落等問題,李峰等[25]提出一種對板材端部預加工出一定形狀的凸齒、孔洞或凹槽,將處理后兩板材的連接端部進行匹配搭接,沖頭對連接部位加載使其發生塑性變形,實現板材間的連接。針對不等厚度的不銹鋼板與鋁板進行了板材搭接工藝研究,預先設計好端部形狀,交叉連接后通過模具進行壓縮連接。利用有限元模擬軟件DEFORMTM–3D 模擬了連接過程,試驗與仿真結果較為吻合 [26]。Pragana 等[27]提出了一種通過局部切口、彎曲和板料壓縮獲得搭接接頭的新方法(圖6),對該接頭工藝參數進行了試驗與模擬研究,獲得的搭接接頭表面無凸起,但連接過程較為復雜。圖5 激光沖擊鉚接工藝原理及連接件
Fig.5 Schematic diagram of making interlock by laser shock forming and obtained clinched joint圖6 新型板材搭接接頭連接工藝
Fig.6 A new joining by forming process to produce lap joints“榫卯結構”是古代建筑中木構件的一種常用連接方式,近年來,“榫卯結構”也被逐漸應用于金屬板材間的連接中。Silva 等[28]提出了一種將切縫剪切與板料體積壓縮相結合的成形連接工藝,用于制造作為能量吸收器的薄壁防撞箱,比較了新型防撞箱與傳統點焊防撞箱的整體耐撞性能,結果表明,這種焊接工藝可以很好地替代電阻點焊。Bragan?a 等[29]提出了一種室溫下垂直板材間的“榫卯”連接方法,基本原理為在平板上預制矩形孔(卯),在垂直板端部預制突出的榫頭,將榫頭穿過矩形孔后采用模具對其端部壓縮,從而實現二者間的連接。但該方法在連接部位仍存在突出部分,在對連接件外觀要求嚴格的表面仍難以滿足要求。針對該問題,Silva 等[30]提出了一種兩步法獲得垂直板材間連接接頭的方法,其原理和獲得的連接件如圖7所示,首先通過在厚度方向部分壓縮其中一塊板來獲得階梯型的榫槽,然后通過在垂直于榫槽厚度的方向上鐓粗榫頭,以完全填充榫槽,采用該方法可獲得表面平整的接頭。對于平行板材間的連接,榫頭無法像垂直板材間通過去除材料的方式制造,Silva 等[31]提出一種電弧熔絲增材制造與塑性成形相結合的方法來獲得板材間的搭接接頭,上部板材預制榫槽,下方板材通過電弧熔絲增材制造的方法制造榫頭,然后壓縮榫頭實現平行板材間的連接。該方法可以獲得任意形狀和厚度的榫頭,拓寬了工藝適應性。Baptista等[32]提出了一種金屬–聚合物三明治復合板搭接接頭制造新方法,其成形過程及獲得的搭接接頭及剖面如圖8所示,通過在金屬–聚合物三明治復合板鉆盲孔,去除表層的金屬板和中間層的聚合物板,然后在二者之間盲孔部位放置金屬鑲塊并壓縮使其變形,從而獲得三明治板材的搭接接頭,表面無凸起。板材–管材塑性連接新方法
板材與管材間的塑性連接方法可以歸納為兩種主要方式:(1)在管材端部制造環形法蘭,將板材放置于法蘭上,再對管材端部進行壓縮,實現二者的固定和連接;(2)通過壓縮管材,使其發生失穩起皺,實現對板材的固定和連接。圖7 “兩步法”垂直板材間連接方法
Fig.7 Two-stage joining of sheets perpendicular to one another圖8 金屬–聚合物三明治復合板搭接接頭成形過程
Fig.8 Joining by forming process to produce lap joints in metal-polymer sandwich composite sheetsAlves 等[33]在板材–管材塑性連接工藝上進行了大量的探索,提出了一種在室溫下通過塑性變形將管與平板固定的連接工藝,其原理如圖9所示,主要是通過對管材端部進行局部擠壓形成凸臺,將板材置于凸臺上后,再通過擴口模對管材端部施壓,從而實現管材端部與板材之間的連接,通過該方法獲得了鋁合金管與鈦合金、鋼和聚碳酸酯塑料的連接件。該工藝的難點在于制造環形法蘭過程容易出現折疊或破裂等缺陷,而且該方法中法蘭是尖角的,對于連接強度存在一定影響。鑒于此,Alves 等[34]提出了一種新的薄壁管環形法蘭制造工藝,采用新型凹模和上、下模具同時運動的方式獲得優化的凸臺。采用該方法成功制備了金屬聚合物夾芯復合板與金屬管的連接件[35]。在此基礎上,在板材待連接處預制沉孔,進而獲得端部更為平整的連接表面,并研究了不同沉孔尺寸對連接效果的影響規律[36]。他們還提出了一種利用薄壁管受壓后產生塑性失穩波紋,實現板材與管材間連接的新室溫連接工藝,可以作為現有緊固件機械固定、焊接和結構膠接之外的一種低成本、高效替代連接技術[37]。為了進一步提高連接效率,提出了采用單行程沖壓成形管材,將板料固定于管材上。該方法是一種靈活、經濟的機械連接工藝,采用該工藝獲得了不同材料間的連接、凸輪軸、座椅靠背框架結構等(圖10)[38]。為了達到在板材與管材任意位置的快捷連接,且保證表面美觀程度, Alves 等[39]提出了一種基于板材周向擠壓的連接工藝,通過擠壓緊鄰管材部位的薄板,材料沿內徑方向塑性流動使得管材縮頸變形,實現二者的快速連接。將試驗和有限元建模相結合,確定了主要工藝參數對塑性流動中的影響,并分析了完好和失效接頭的不同變形模式。傳統的擠壓工藝也被應用于軸套連接中,通過擠壓芯軸使其發生塑性變形而實現連接,如圖11所示,然而接觸面上產生的非均勻接觸應力分布影響到連接強度。為此,Meissner 等[40]采用數值模擬方法獲得擠壓連接工藝中需求的制造精度和工藝窗口。Kitamura 等[41]提出一種室溫下軸與法蘭的擠壓連接方法,先在室溫下通過鋸齒模具擠壓,在軸的端部制造鋸齒,對鋸齒部分進行滲碳和淬火處理提高硬度,然后軸的鋸齒端部作為模具擠壓進入預制孔的法蘭中,對法蘭孔內徑材料進行去除,并實現二者的連接。采用該方法獲得的連接件的屈服扭矩為采用機械組裝方法的1.5倍。圖9 依靠薄壁管體積成形實現板–管連接
Fig.9 Sheet-bulk forming of thin-walled tubes for joining applications圖10 連接件示例
Fig.10 Examples of joining applications圖11 軸套徑向擠壓連接
Fig.11 Shaft-hub connection joined by lateral extrusionAgrawal 等[42]提出了一種通過管材末端卷曲實現板材–管材連接的方法,其原理如圖12所示,通過試驗與有限元分析,發現成形參數中模具圓角半徑、摩擦條件和管支架長度對接頭質量有重要影響。但是,該方法會在連接處產生卷圓,不適用于對連接端面表面質量要求高的情形。Park 等[43]探索了采用電磁成形方法對板材和管材進行連接,其原理及獲得的鋁合金板–管連接件如圖13所示,瞬間的高壓脈沖磁場迫使管材局部發生變形,依靠管材上側的翻邊和下側的脹形實現二者的連接,研究了不同電壓對連接強度的影響,當脈沖電壓大于9.2kV時,獲得了連接完好的Al6063 管與7075 板的連接件。管材–管材塑性連接新方法
Zhang 等[44]采用旋鍛工藝實現了不同直徑的銅管間的塑性連接,其原理如圖14(a)所示,利用有限元模擬軟件Forge 2D 建立了旋鍛成形模型和拉伸試驗模型,研究了成形參數對連接管拉伸強度和連接機理的影響規律。通過光學顯微鏡觀察到的接頭微觀結構如圖14(b)所示,金屬流線在接頭處是連續的,沿管軸向方向排列整齊。連接管的間隙很小,在宏觀上幾乎是無縫的。液力脹接技術是通過對管材內部的液體介質施加精確內壓,使管材與套環產生局部變形,進而實現二者一次性整體裝配的工藝方法,具有工藝簡單、結合面加工精度要求低、材料適應范圍廣、一致性好等優點。圖15為液力脹接的工作原理,主要通過軸管和套環的彈塑性變形和彈復后的殘余應變形成過盈配合,實現二者的脹接,該工藝被應用于發動機空心凸輪軸裝配件(圖16)和油氣輸送用不銹鋼–碳鋼復合管的制造[45–46]。Liu 等[46]研究發現凸輪采用非圓形孔可以提高連接強度,采用合適的內壓和凸輪孔尺寸,與采用圓形內孔的凸輪相比,抗扭強度可近似增加2倍,達到工作扭矩要求的3~5倍。Müller[47]和Weber[48]等采用液壓脹接工藝對橢圓形管和矩形管進行連接,并應用于輕質框架結構的制造中。通常液力脹接是從管材內部施加液壓力,但是對于復雜輪廓管件的連接,模具的放置及液壓的施加等較為困難。Weber 等[49]提出從管材外部施壓,實現管材間的液力連接,并引入最大彈性應變值作為連接的關鍵參數,大大拓展了該工藝的適用性和應用范圍。圖12 通過卷邊實現板–管連接工藝
Fig.12 Joining a tube to a sheet using end curling圖13 板–管電磁連接工藝原理
Fig.13 Principle of sheet-tube electromagnetic joining圖14 采用旋鍛連接實現不等徑間管連接工藝
Fig.14 Joining tubes with different diameters by rotary swaging磁脈沖連接技術屬于電磁成形的一個分支,常見的管件磁脈沖連接系統示意圖如圖17所示,是利用漸進脈沖電磁力對金屬管進行連接的一種高能率、高速率加工方法,可以實現同種金屬或異種金屬、金屬與非金屬間的連接,連接界面不會發生融化,從而能夠保持材料的原有特性。與傳統焊接工藝相比,磁脈沖連接具有效率高、環境友好、適合大批量生產等優點,但同時也存在設備投入大、工藝參數嚴苛、安全防護等級要求高、對連接零件尺寸有限制等問題[50–53]。管路系統被喻為飛機的血管,航空導管的連接性能對于管路系統的安全性和可靠性有著重要影響。張榮霞等[54–55]針對基于扭矩控制的導管內徑滾壓連接工藝進行了研究,該方法的工作原理如圖18所示,芯軸主動轉動,滾柱帶動保持架軸向轉動,依靠芯軸與滾柱間的徑向擠壓力和切向摩擦力,迫使導管材料進入管套凹槽,完成連接過程,研究了成形機理及特點,分析了成形扭矩與連接件管端伸出量和連接件內徑的關系,并成功制備了TA18 鈦合金導管連接件,裝配面的密接度滿足設計要求。張凌云等[56]采用聚氨酯橡膠擠壓實現航空液壓導管接頭的連接,采用有限元分析方法研究了脹形壓力、聚氨酯橡膠套厚度與長度、導管與管套的間隙等工藝參數對于連接質量的影響,并采用優化參數獲得了連接質量良好的導管接頭,對實際生產起到了重要的指導作用。Alves 等[57]提出了一種實現管材端部簡單快速的連接方法(圖19),先利用外層管材的脹形實現管材端部的搭接,然后沿管材軸向進行壓縮,搭接部位兩層管均發生塑性失穩,壓合后實現互鎖。采用該工藝實現了S460MC 碳鋼管的連接,并結合有限元方法確定了影響連接質量的兩項工藝參數:開口間隙與管材半徑的比值和管材初始無支撐高度比值。另外,該方法也同樣適合于異種材料間的連接[58]。圖15 液力脹接原理
Fig.15 Principle of hydrojoining圖16 采用液力脹接制造汽車發動機空心凸輪軸裝配件
Fig.16 Assembled hollow camshaft for truck engine by hydrojoining圖17 管件磁脈沖連接系統
Fig.17 Magnetic pulse welding set up for two tubes圖18 內徑滾壓連接技術
Fig.18 Principle of inner diameter rolling connectionSilva 等[59]對管端部連接工藝進行了改善,主要是對上、下模增加了環形凹槽,可以實現連接管之間更好的定位,同時搭接部分長度更長,且帶有平直段,在輸送液體或氣體時也可以使用。拉伸、扭轉、彎曲和密封性破壞試驗結果表明,新的“搭接”接頭的性能均勝過“對接”接頭。然而上述方法會在連接部位外端產生環形的凸起,影響到產品外觀和美觀性。Alves 等[60]提出一種通過內部機械互鎖實現管材間塑性連接的方法,此方法會在管內部形成凸起,外部無凸起,美觀性有了一定提升。通過管材塑性失穩的方法,也能夠用來實現不同直徑管材間的垂直連接和傾斜連接,以及三通管的制造(圖20)[61]。Baptista 等[62]將電弧熔絲增材制造技術與塑性成形相結合,通過電弧熔絲增材制造技術在型材交接處制造榫頭,用來制造空心界面鋁型材的十字接頭(圖21),研究表明,十字節點的單元能夠承受2kN的拉脫力和3.2kN的剪切破壞力,可用于制造低成本鋁材結構件,在公共汽車、火車或輪船等客運車輛上具有潛在的應用。圖19 管材連接工藝原理及連接件截面
Fig.19 End-to-end joining of tubes by plastic instability圖20 基于薄壁管塑性失穩獲得的管–管連接件
Fig.20 Application of the new proposed technology based on plastic instability waves in thin-walled tubes圖21 基于電弧熔絲增材制造技術與塑性成形的方管交叉接頭成形
Fig.21 Cross joint consisting of square hollow section profiles obtained by combination of additive manufacturing and joining by forming板材、管材塑性連接技術發展趨勢
未來板材、管材塑性連接技術的研究應主要關注以下方向:(1)注重塑性連接方法與其他工藝的結合。對于某些復雜的連接結構件,單純依靠材料的塑性流動難以實現構件的連接。通過塑性連接方法與沖裁、彎曲、拉深、熱處理等傳統工藝以及增材制造、激光成形、電磁成形等先進工藝的結合,獲得高連接強度的復雜結構,是塑性連接技術的一個發展方向。(2)尺寸、材料性能差異較大的構件間的連接。對于厚度差異較大的構件,強度、塑性差異較大的金屬間或者金屬與非金屬(如工程塑料、復合材料等)間的連接,材料流動不足等問題對傳統的連接方法帶來了挑戰,實現其高效、可靠連接亟需創新連接工藝。(3)專用模具及設備的研發。目前,除了少數鉚接工藝在汽車、航天等領域有著較為成熟的應用,大多數方法還處于基礎研究和驗證階段,距離工程化應用還存在一定差距。塑性連接模具及設備的通用性和操作的便捷性將影響到塑性成形方法的推廣和應用,因此,發展專用模具和設備,對加快新塑性連接方法的推廣及工程化應用具有重要意義。結論
作為傳統螺栓緊固、焊接和膠接工藝之外一種綠色、高效的連接技術,塑性連接技術具有廣闊的發展空間。本文對近年來板材間、板材–管材和管材間塑性連接新方法進行了歸納和論述,近年來國內外提出的板材、管材間的塑性連接技術主要依靠形成互鎖結構,或者利用管材塑性失穩等方式,實現材料之間的有效連接。另外,借助擠壓、沖裁等傳統工藝或增材制造、激光成形、電磁成形等新型成形方法,實現尺寸、性能差異大的構件間的高強度可靠連接也成為一種趨勢。總體來說,大多數工藝仍處于方法的提出及驗證中,需要進一步加大專用設備及模具等的研發來實現進一步的工程化應用。
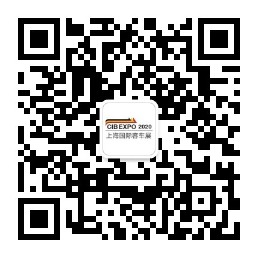
掃碼關注客車制造技術及裝備展官方微信